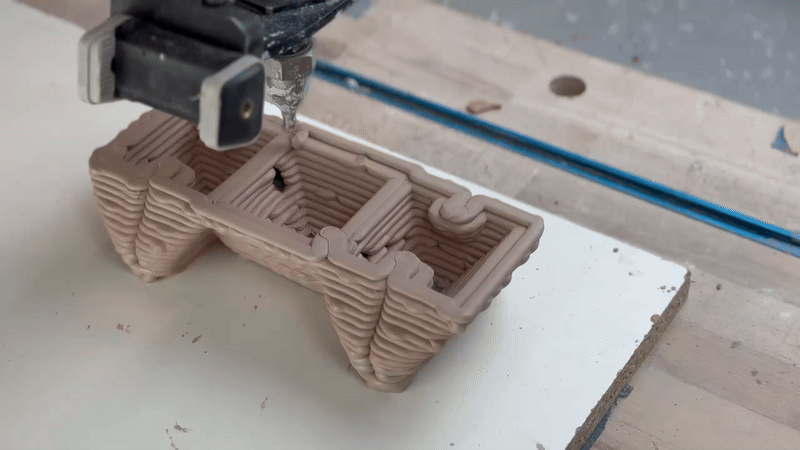
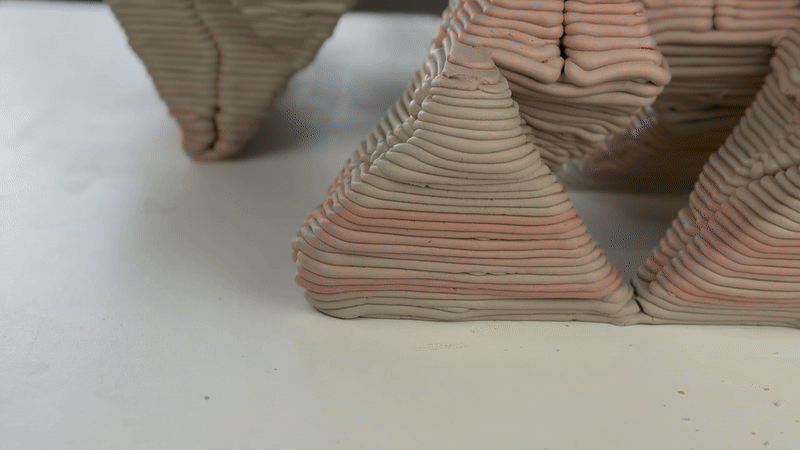
This project explores robotic 3D clay deposition through the lens of space-filling polyhedral structures inspired by Robinson Fredenthal’s sculptures. The first phase involved designing and fabricating modular fused-poly bricks suitable for robotic clay printing, emphasizing geometric precision and material behavior. In the second phase, the research expanded into micro-relief patterning using Convolutional Neural Networks (CNNs), integrating AI-generated textures into the clay-printed surfaces. This fusion of computational design and digital fabrication advances the possibilities of robotic material manipulation in architectural applications.
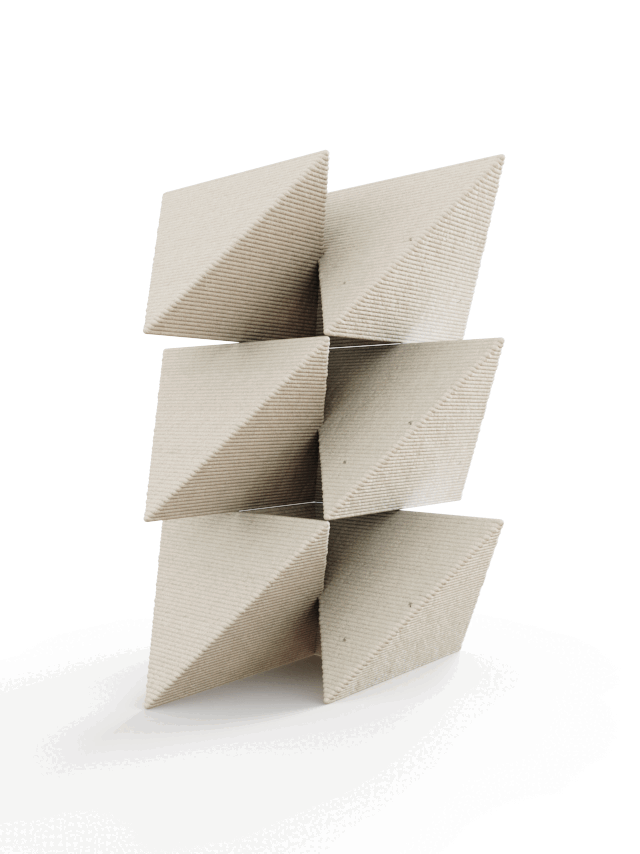
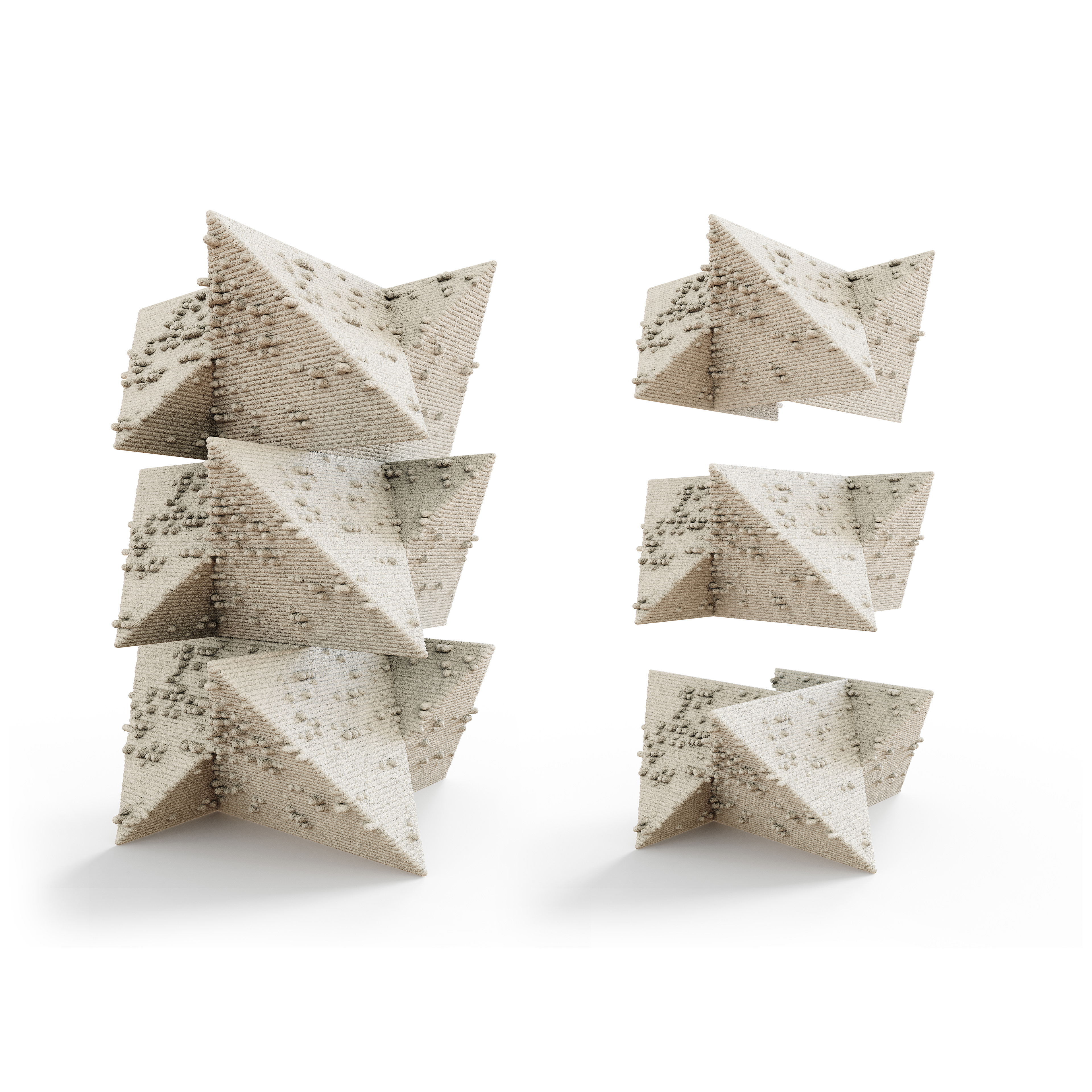
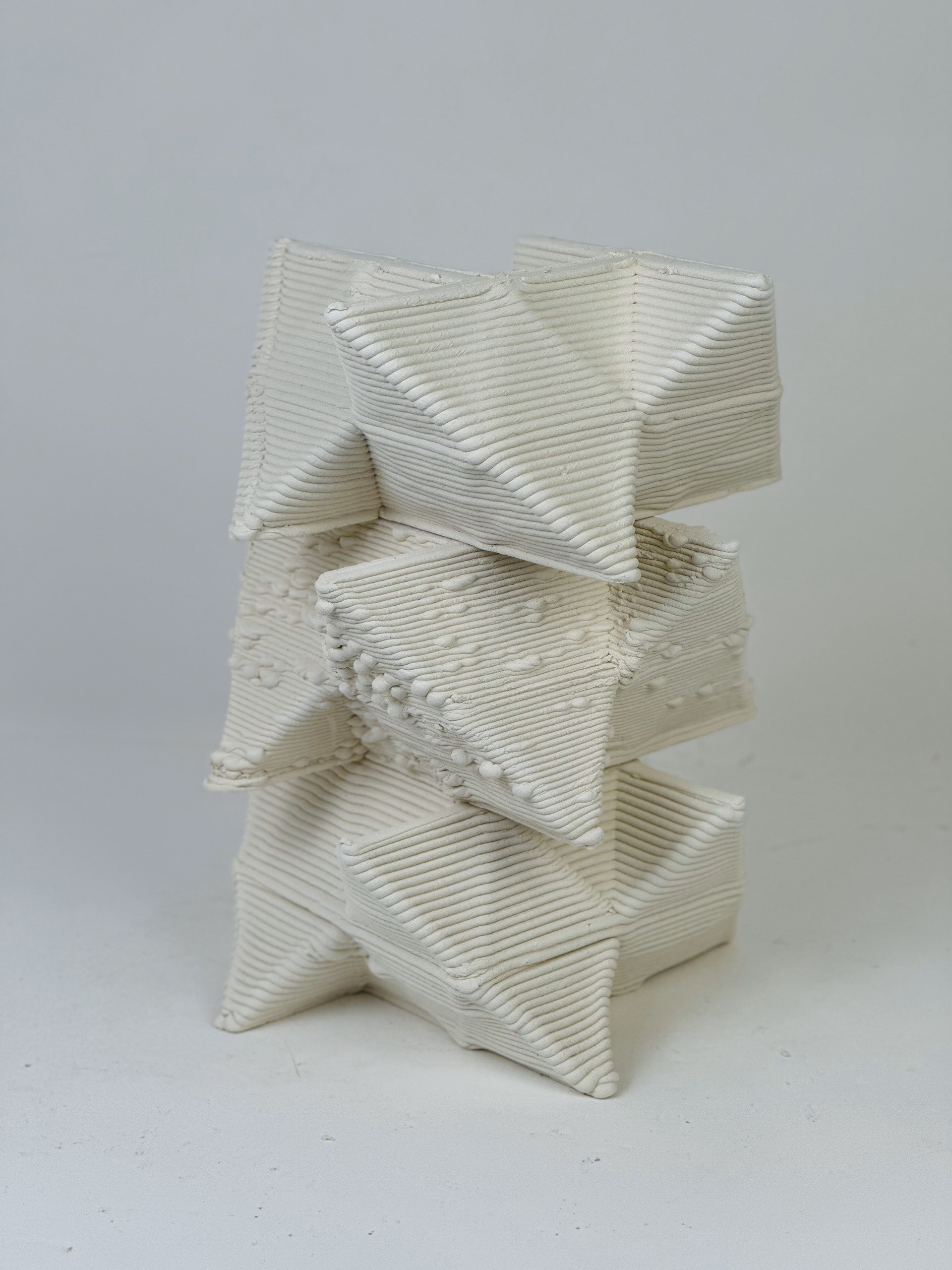
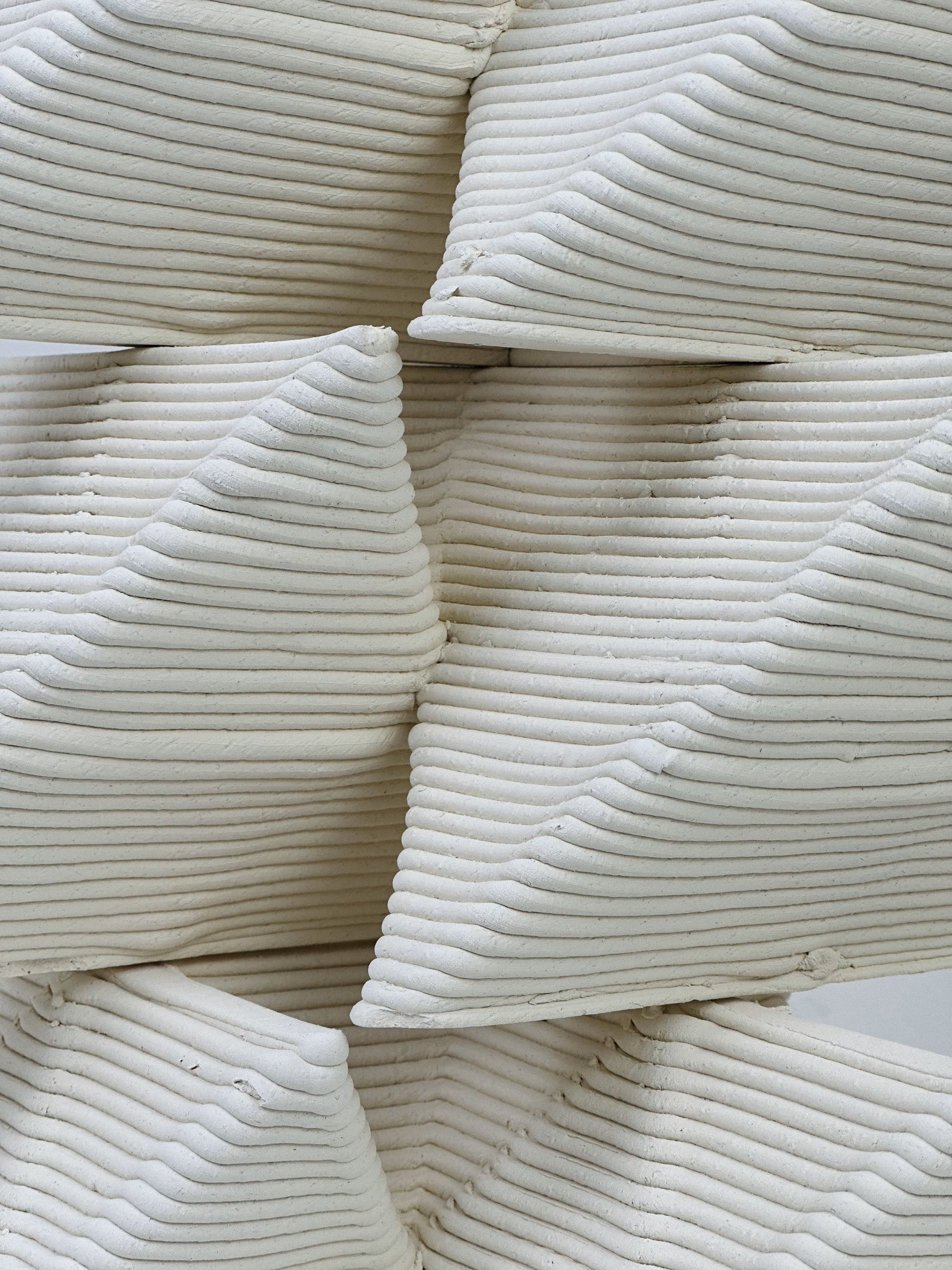
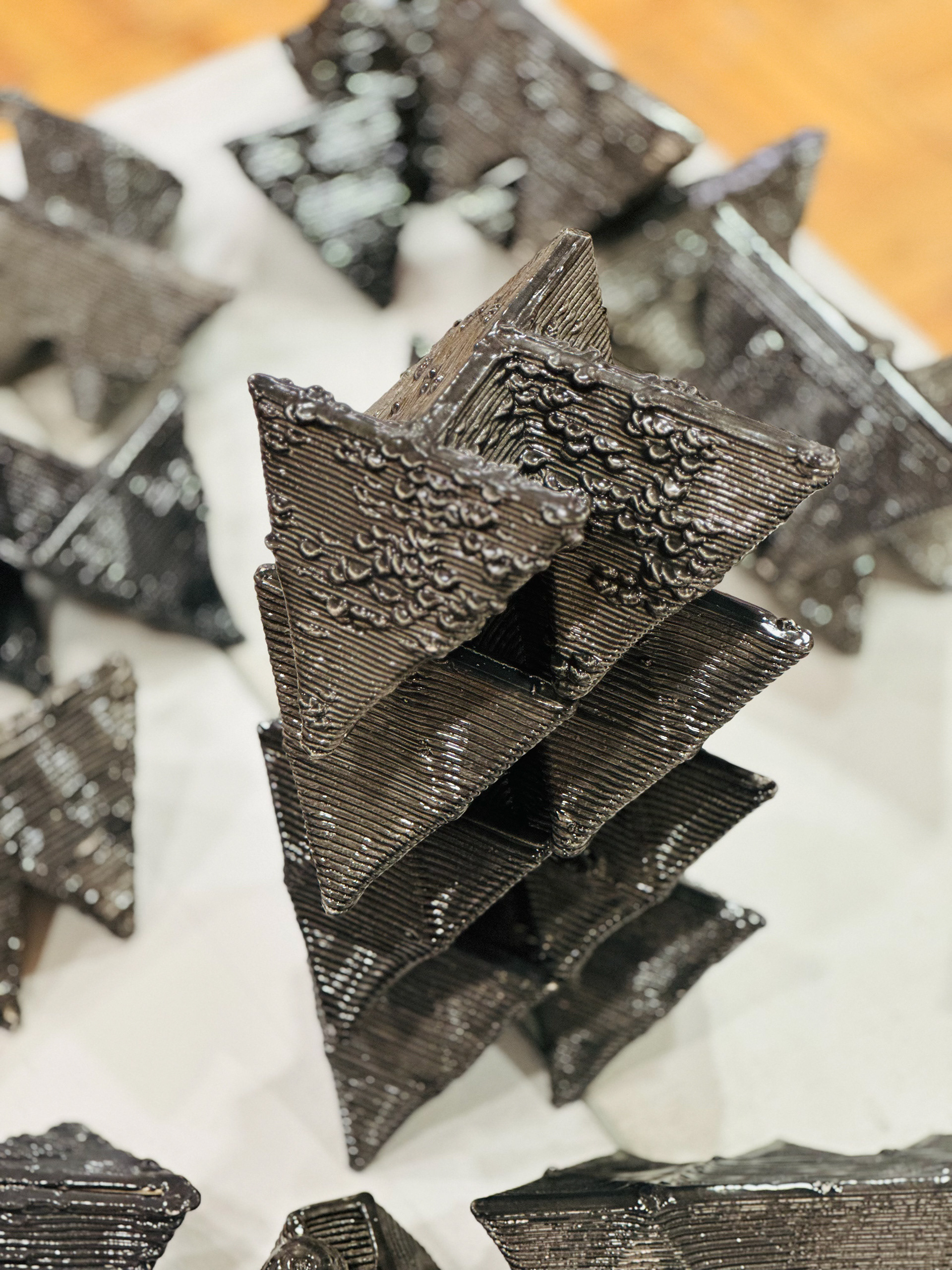
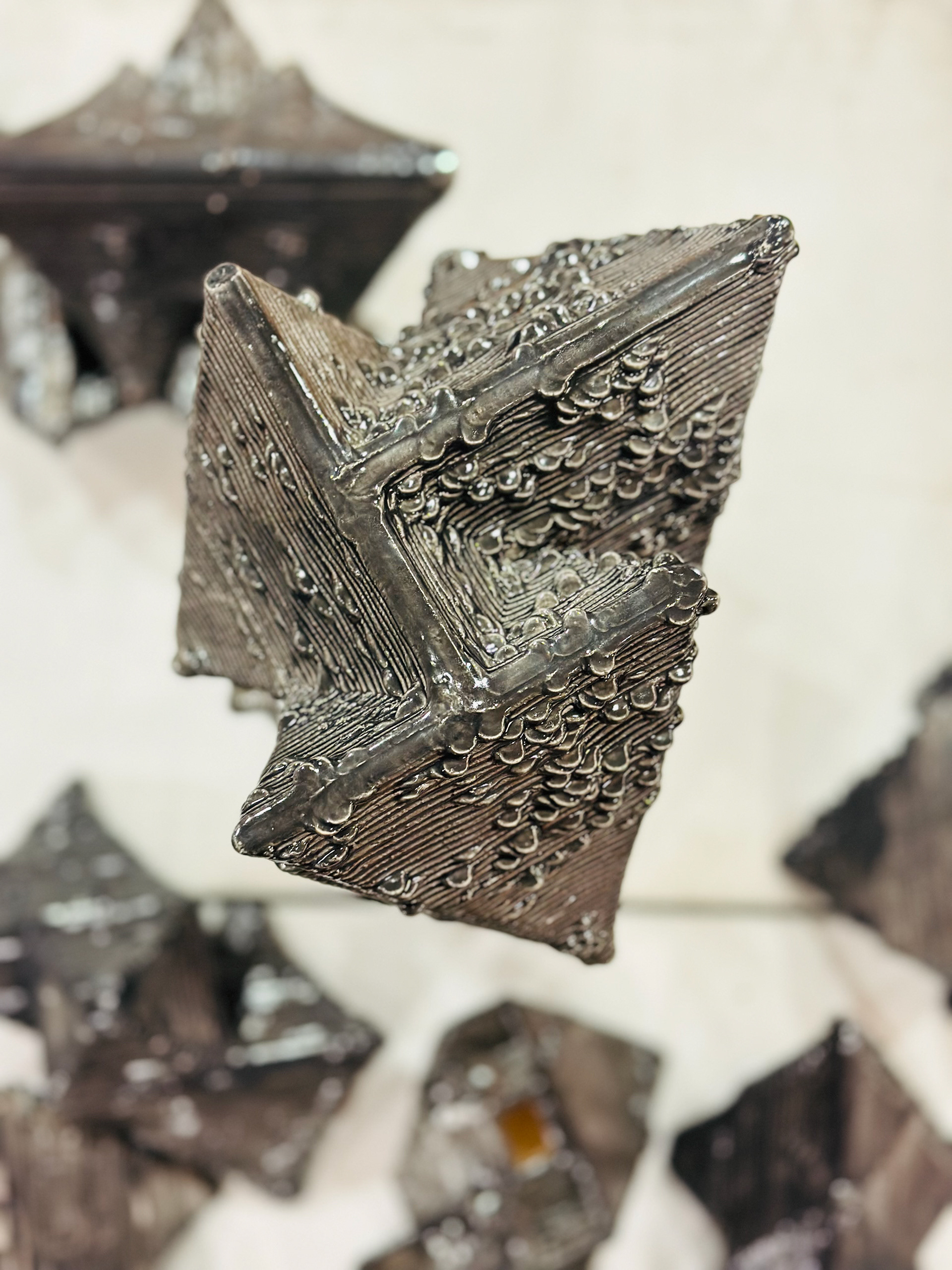
The project investigates the fusion of geometric principles with advanced robotic fabrication techniques, drawing inspiration from Robinson Fredenthal’s sculptural work. At its core, the research explores the spatial relationships between octahedrons and tetrahedrons, leveraging their inherent space-filling properties to generate fused polyhedra. Through computational algorithms, octahedrons are iteratively fitted within tetrahedrons, varying in scale and orientation to create bespoke interlocking structures. Boolean operations introduce curvature, transforming rigid polyhedral forms into fluid, continuous geometries that enhance both structural integrity and scalability.
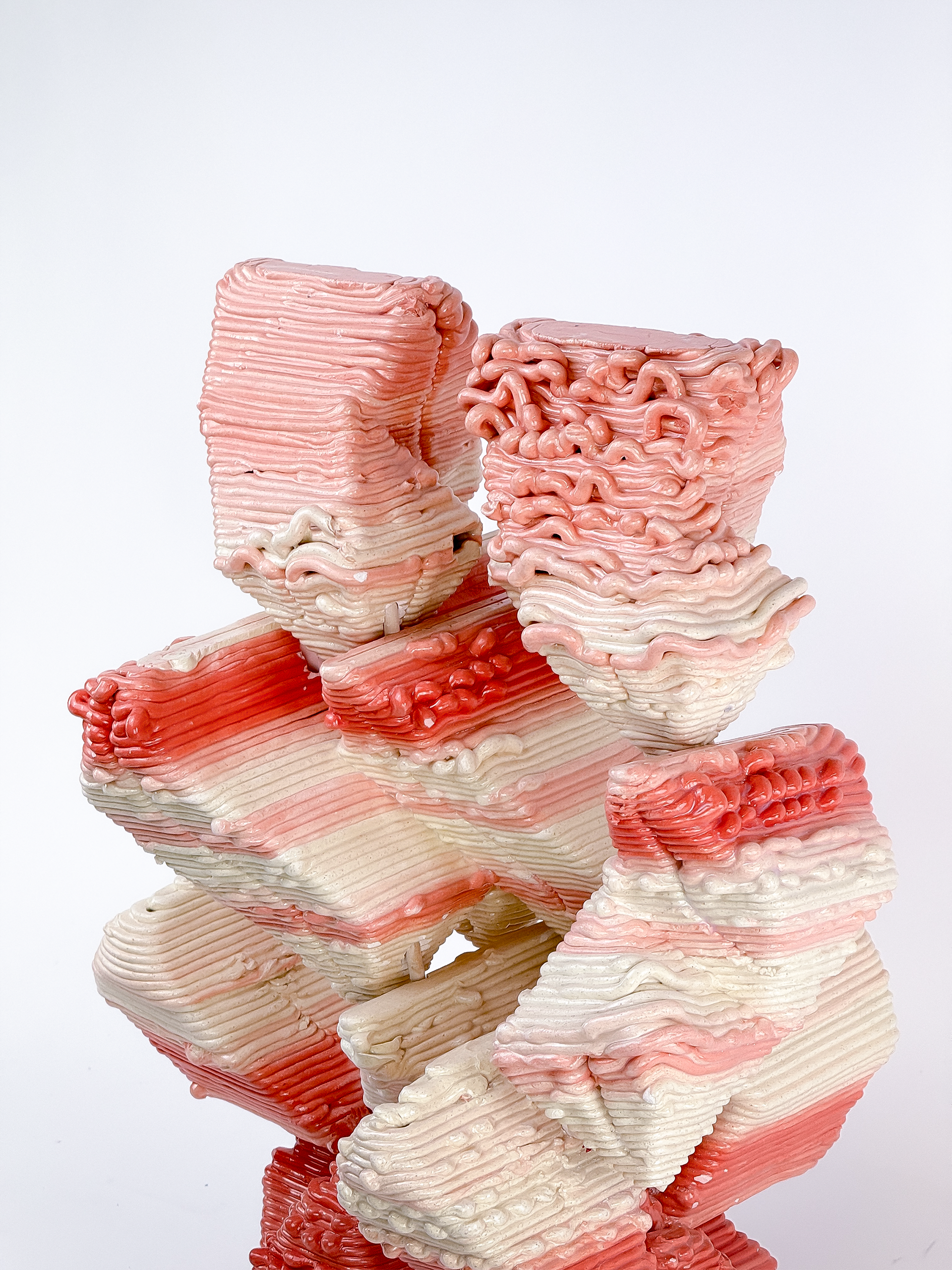
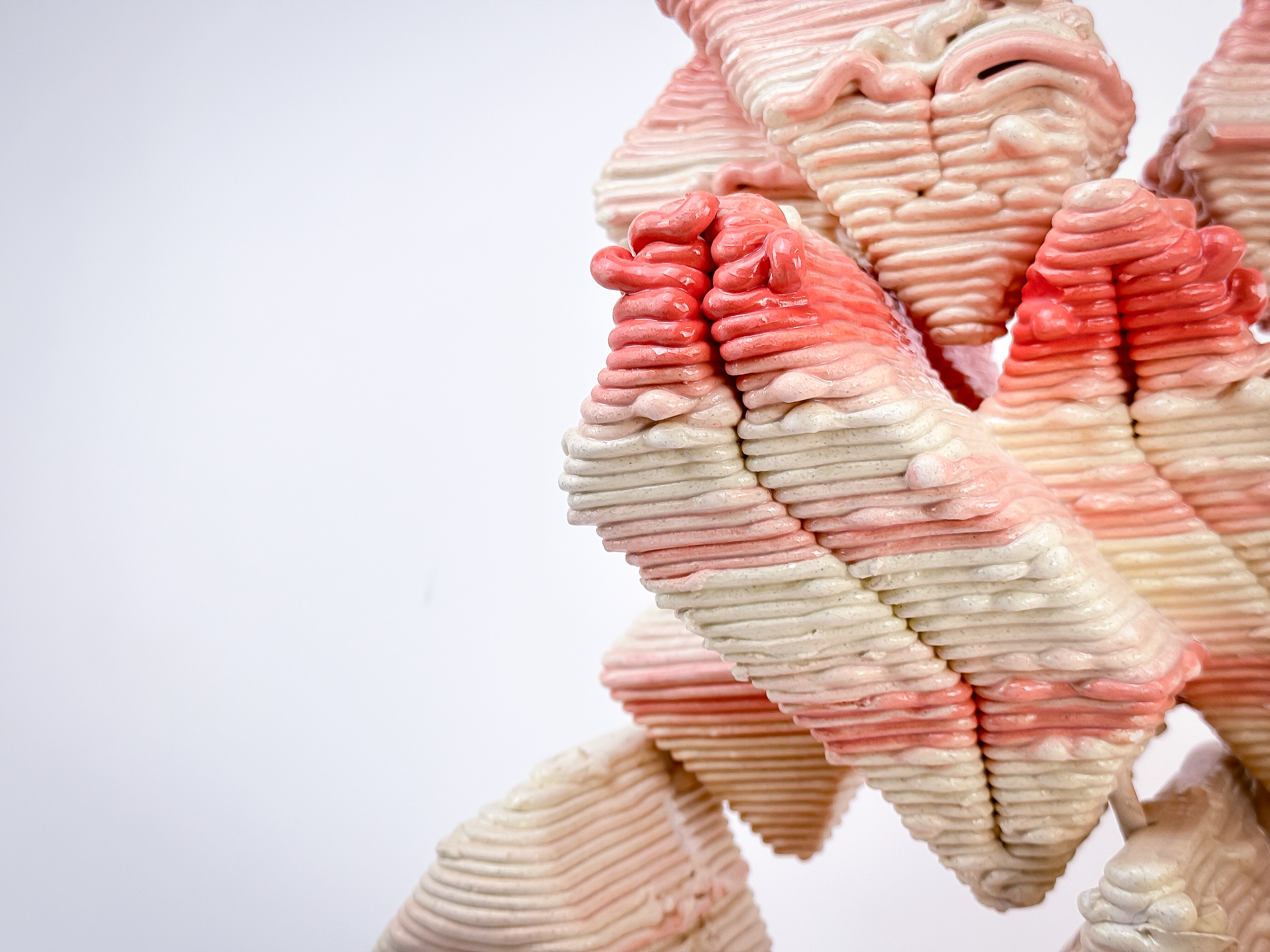
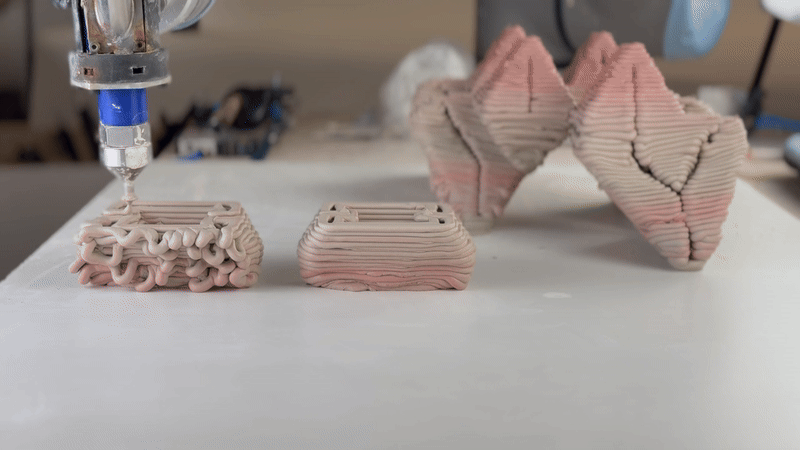

Beyond geometry, the project also explores material innovation by incorporating pigment into the clay mix. Various layering methods are tested to achieve controlled gradient patterns during robotic deposition. One approach involves stacking layers of differently pigmented clay to create precise, gradual color transitions, while another method places pigments vertically, resulting in unpredictable and organic blending. These strategies balance randomness with control, offering new opportunities for both aesthetic expression and material performance in additive manufacturing.
Fabrication challenges arise from the unpredictability of clay behavior during deposition. To address this, an algorithm optimizes the orientation of each component, preventing print failures due to cantilevers and ensuring structural stability. By integrating computational design with robotic clay deposition, the project pushes the boundaries of additive manufacturing, demonstrating how fused polyhedra and pigment-layering techniques can redefine material expression and geometric interlocking in architectural and sculptural applications.
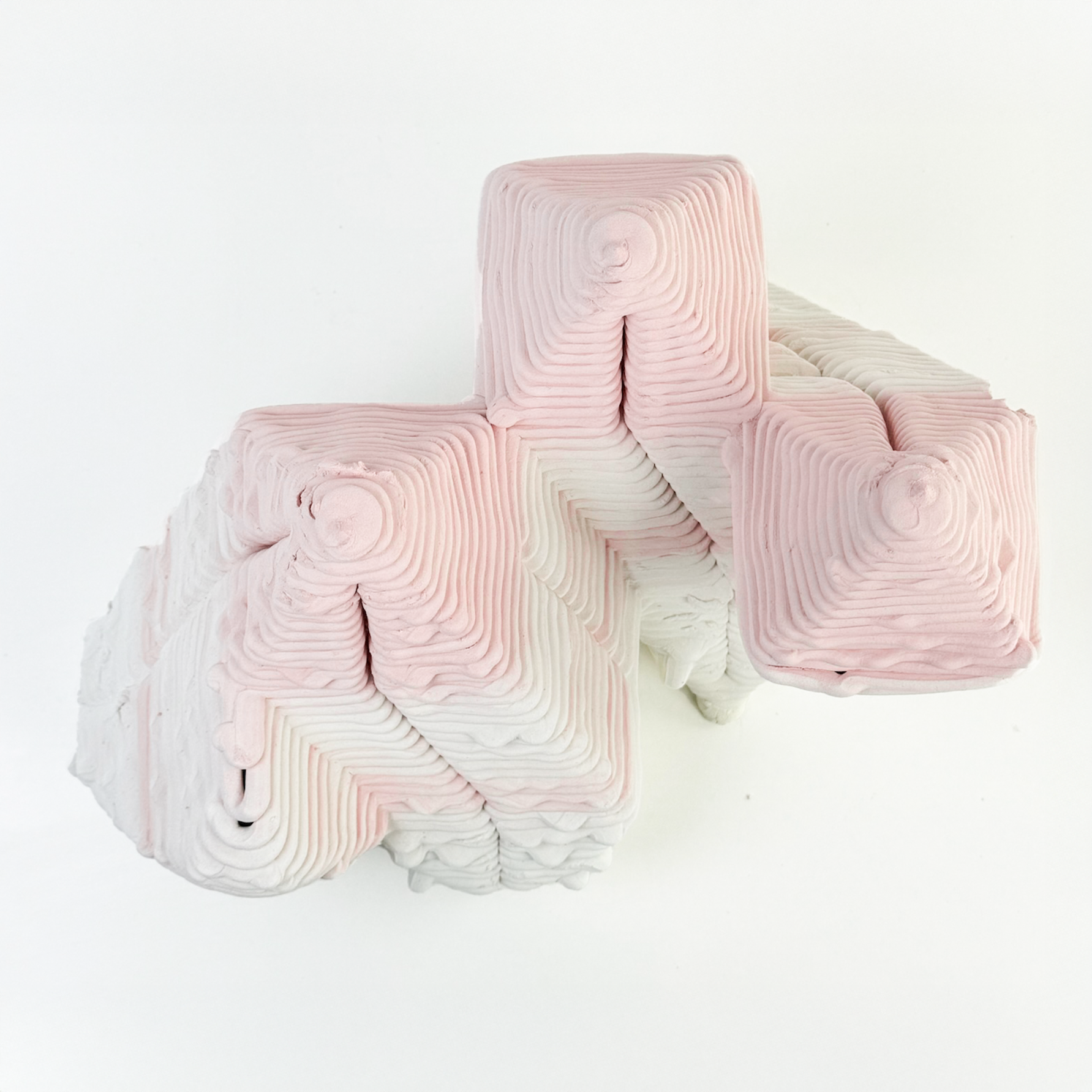
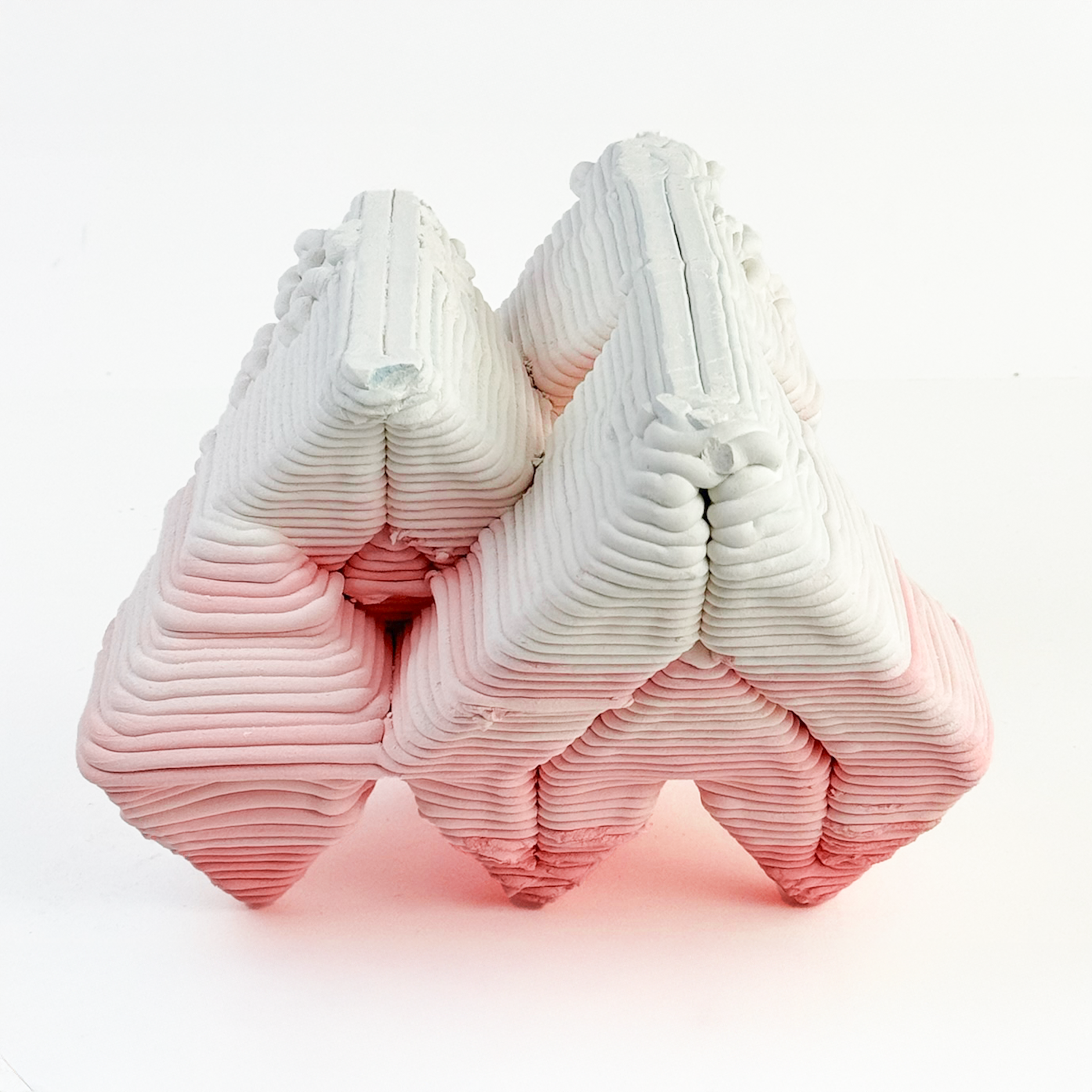
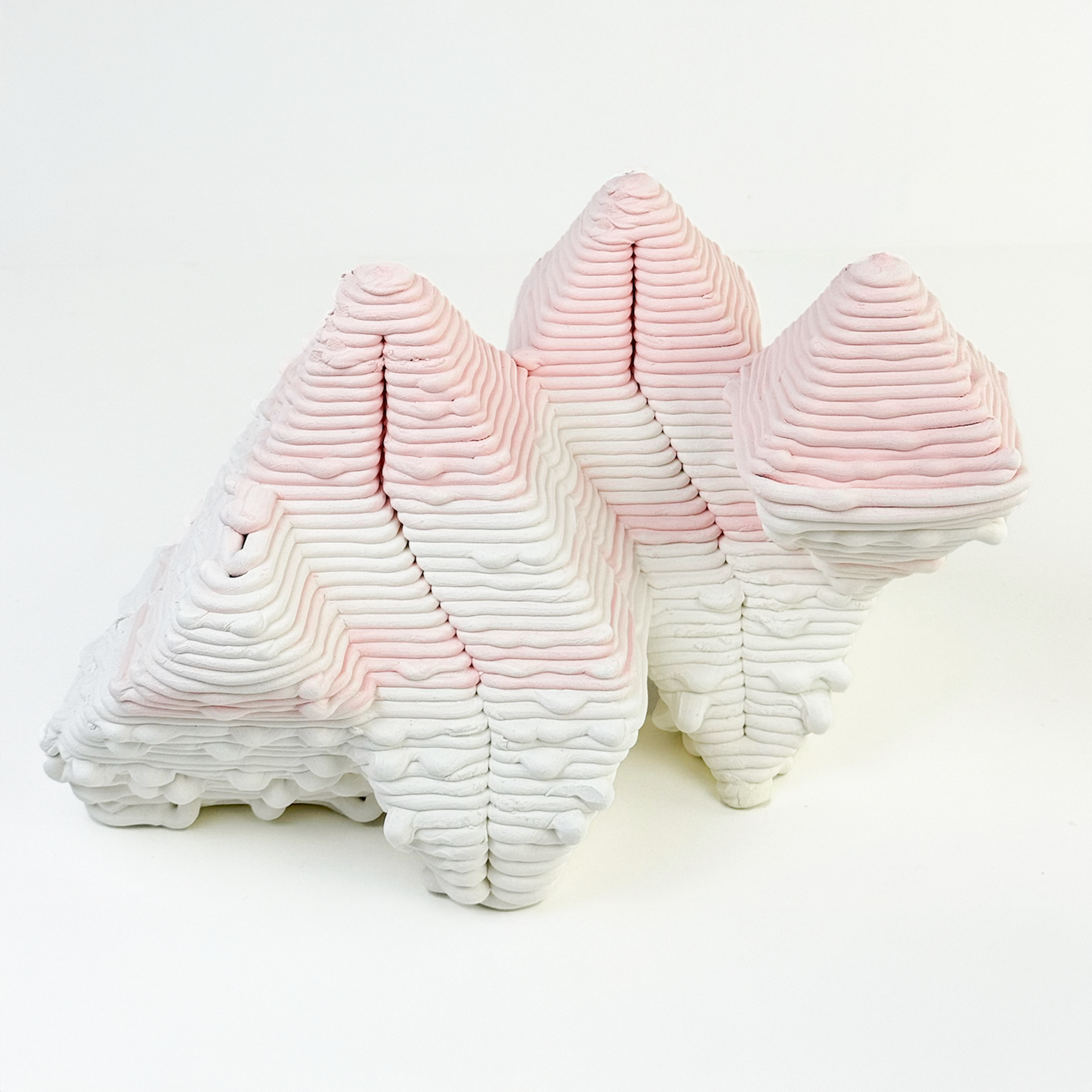
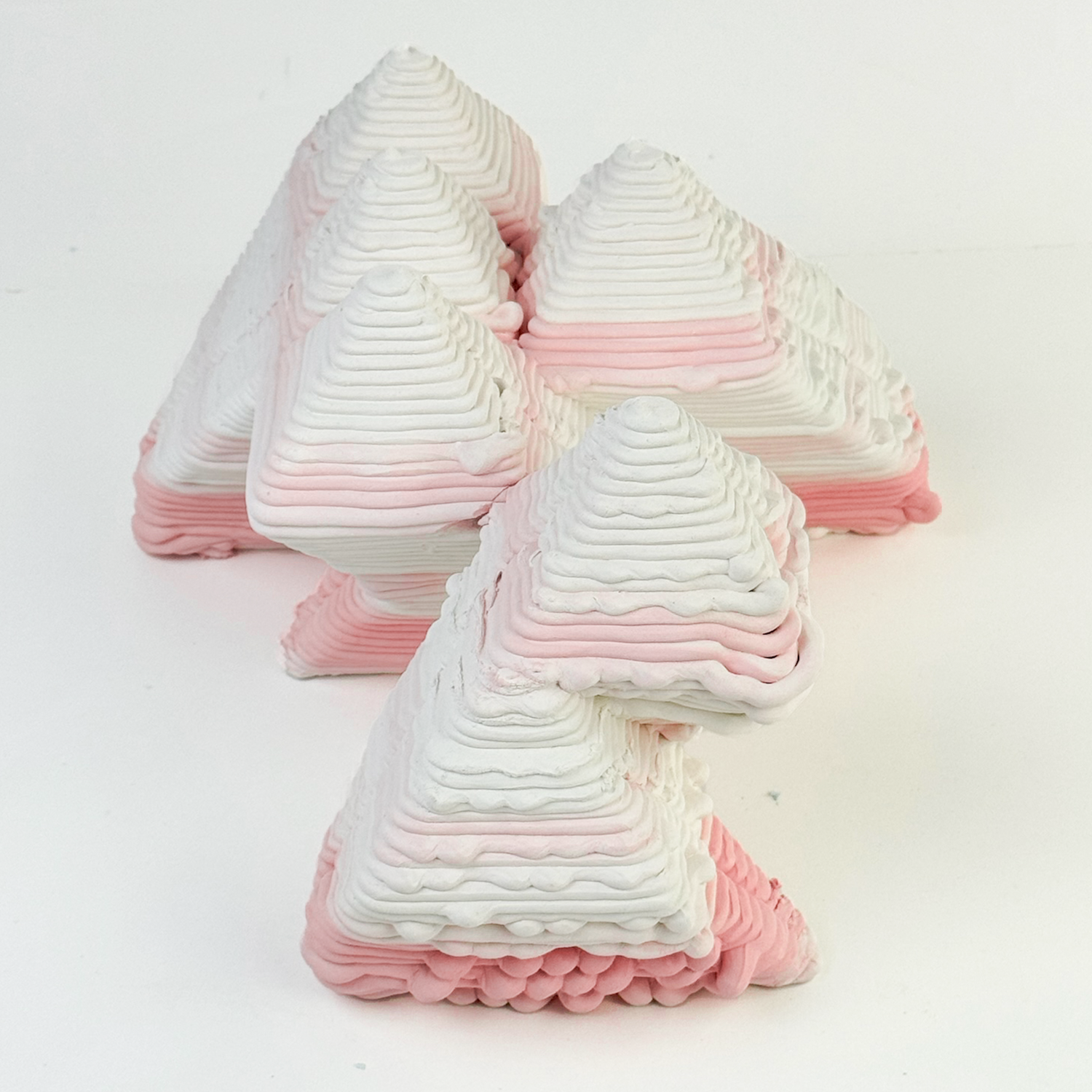
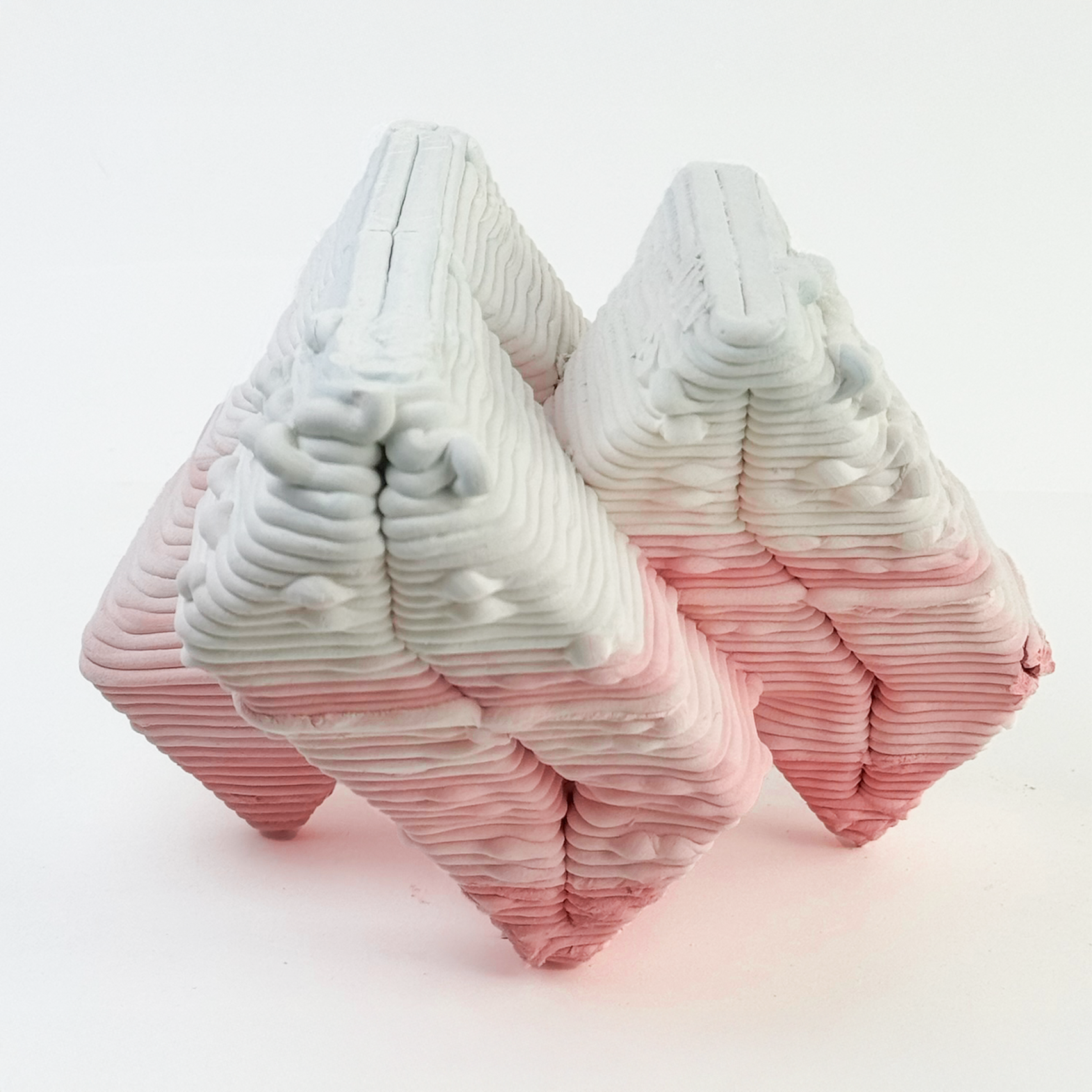
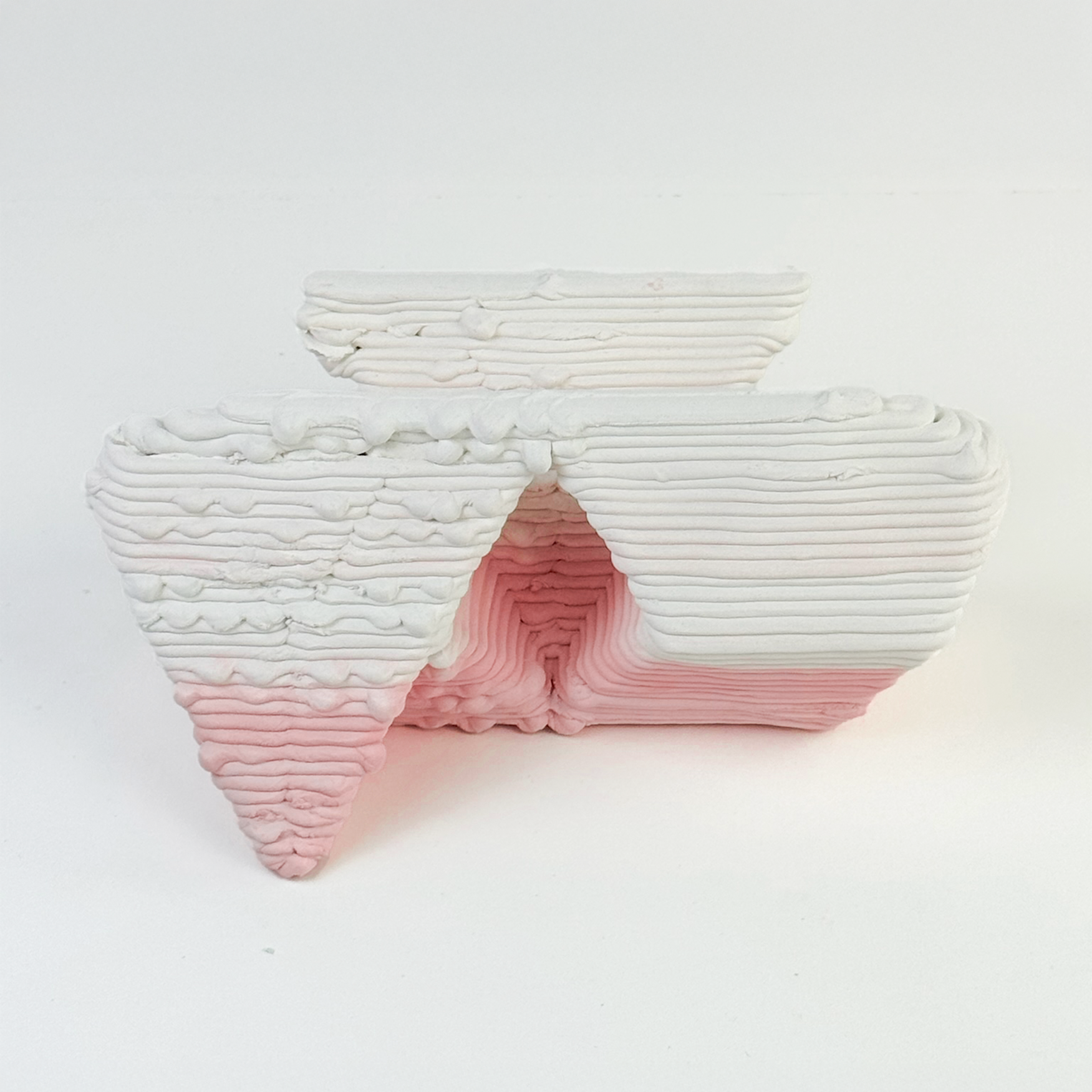
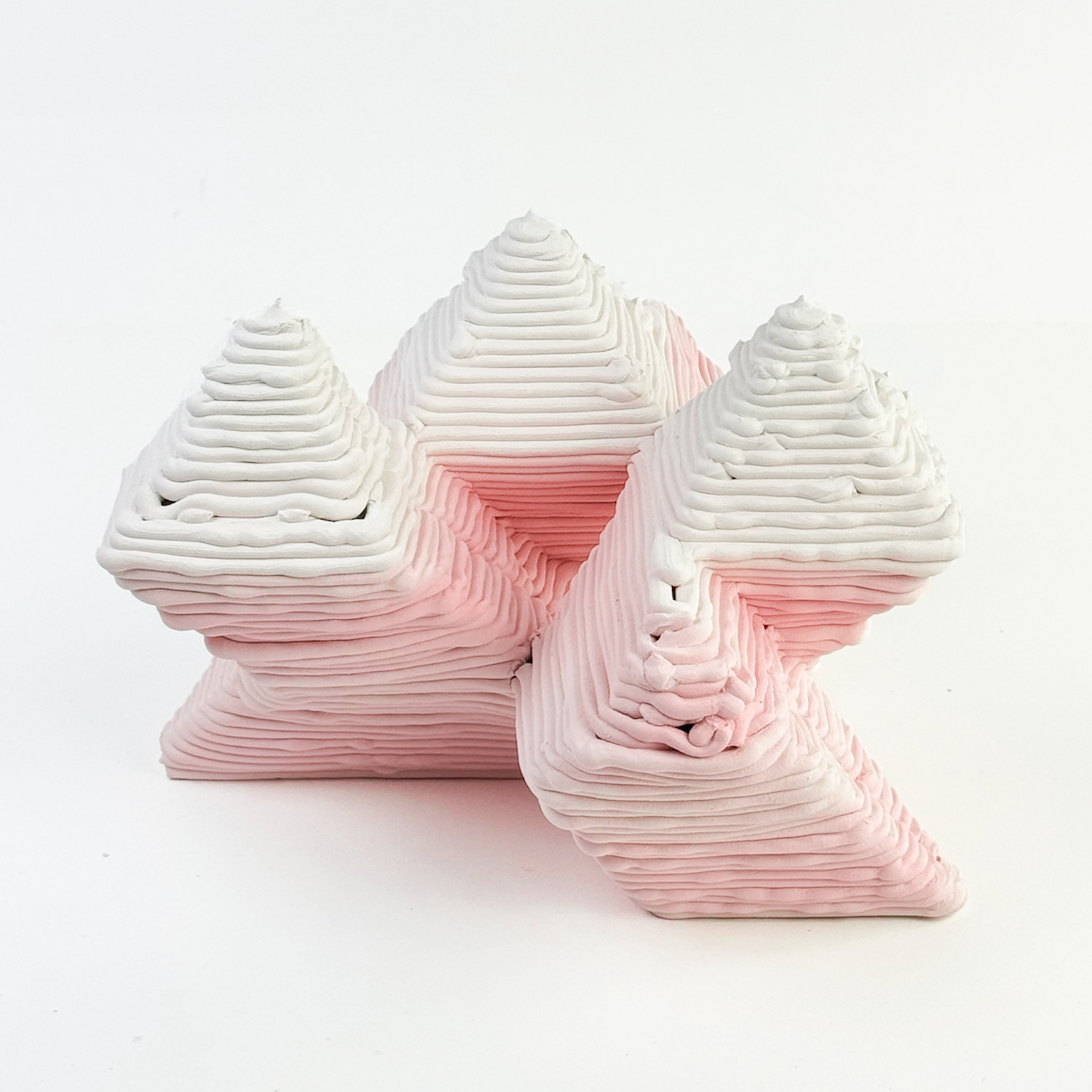
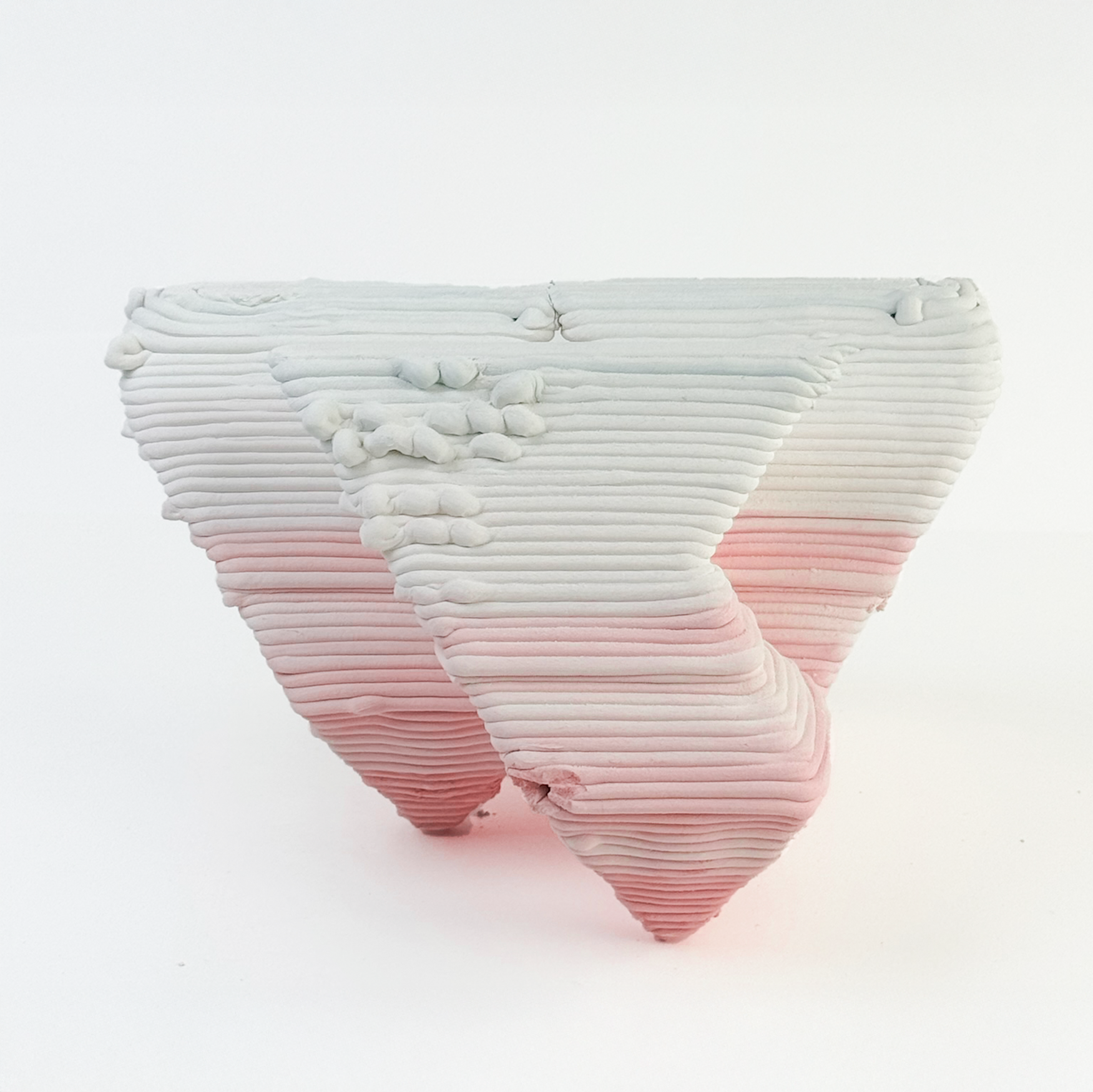
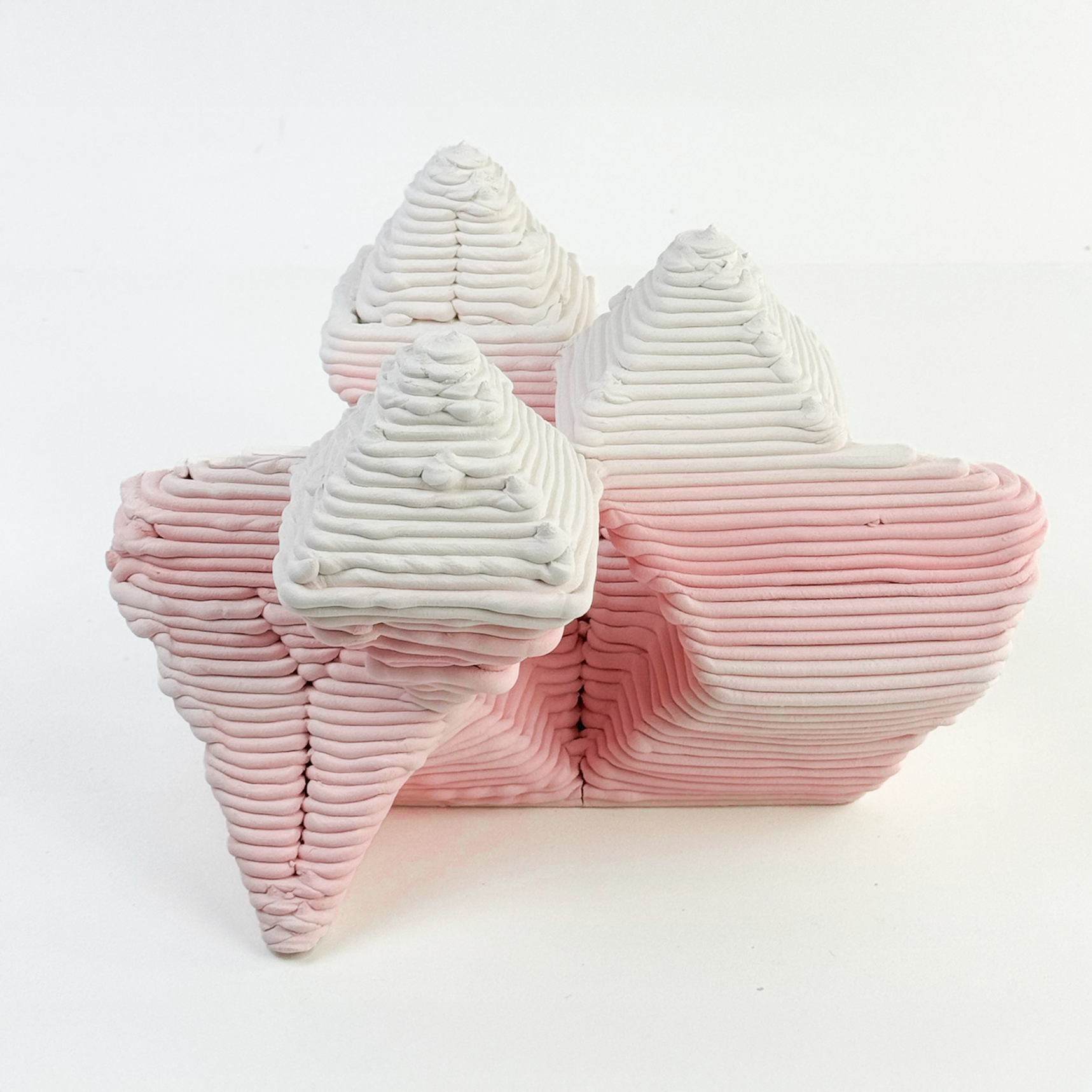
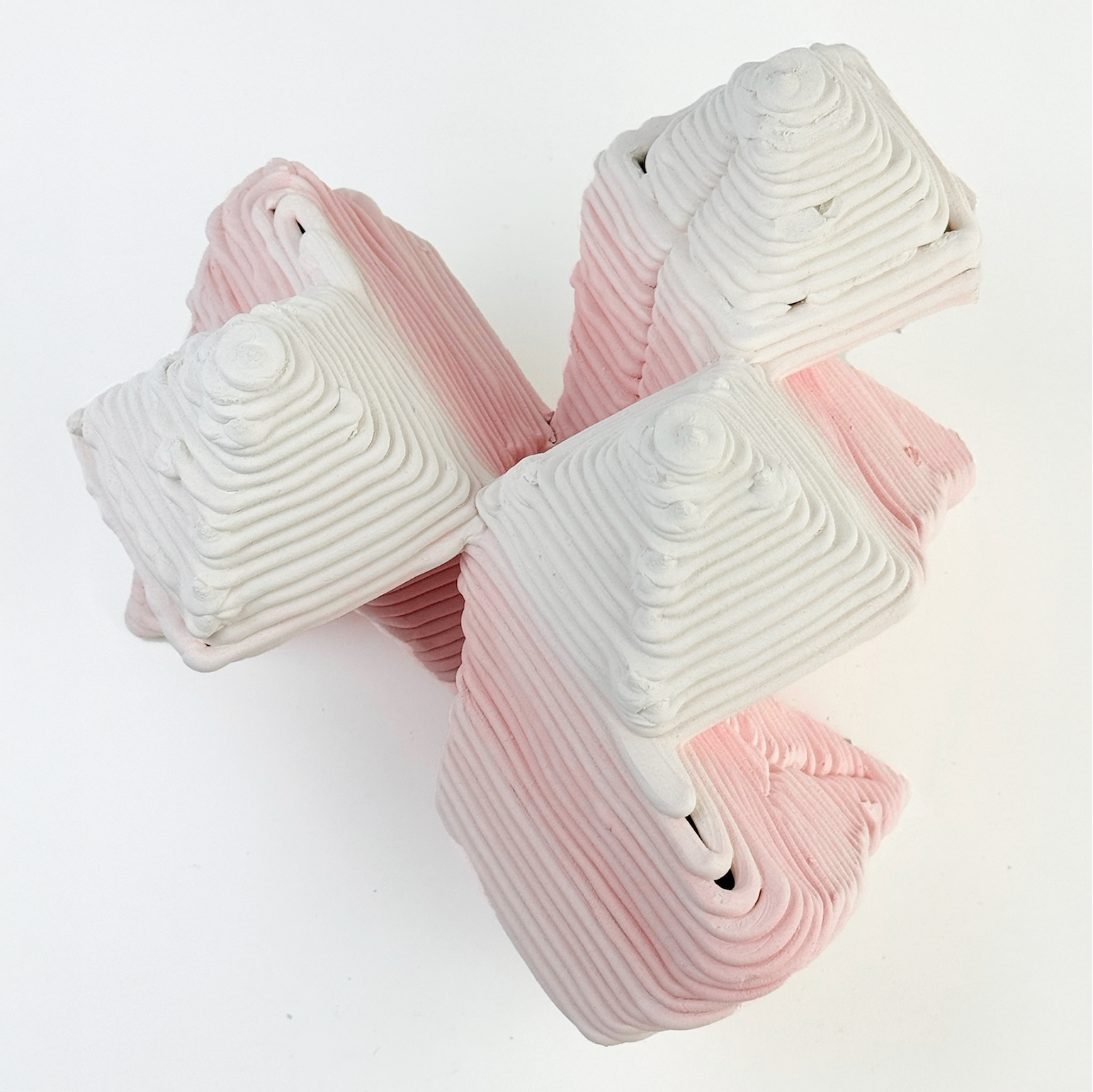
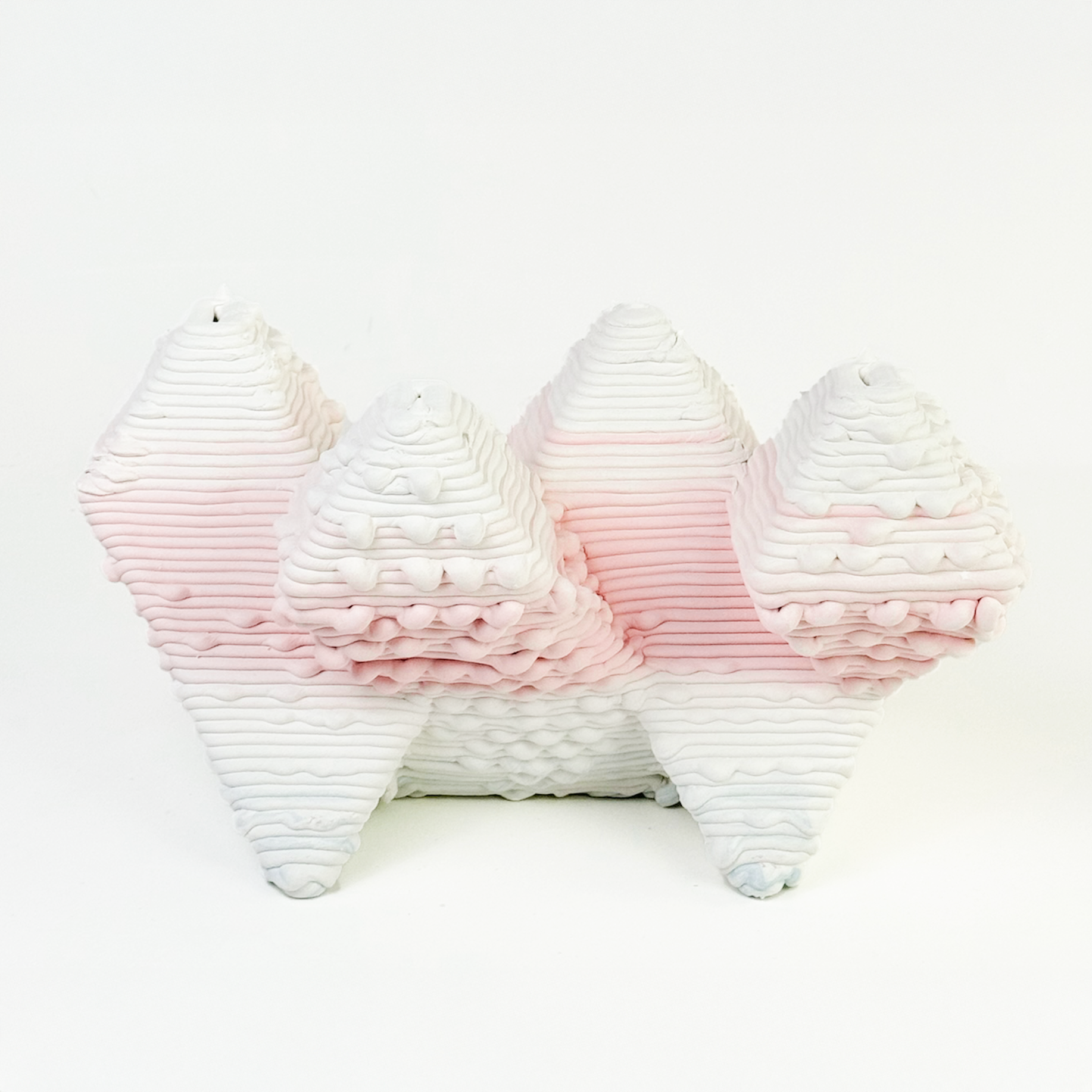
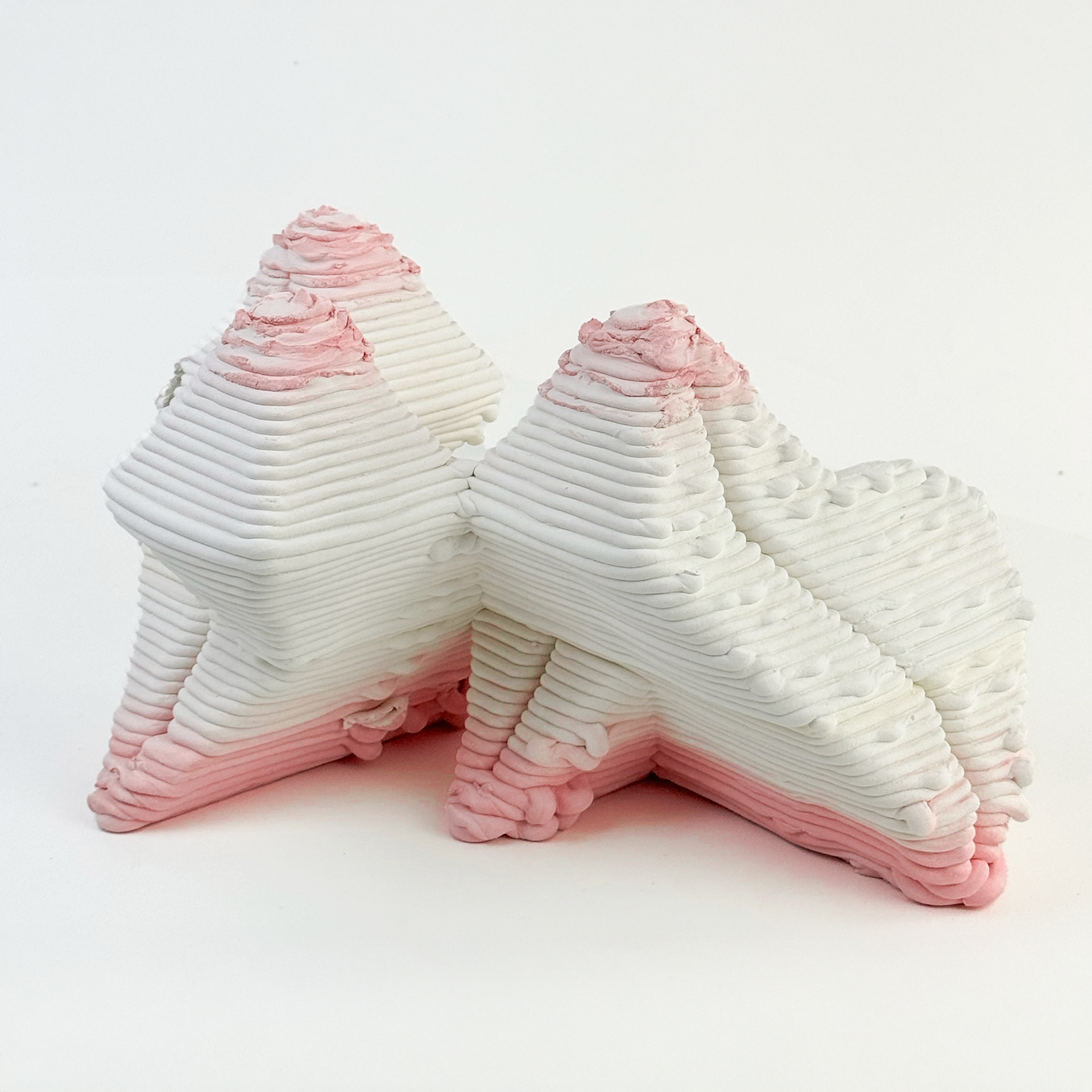
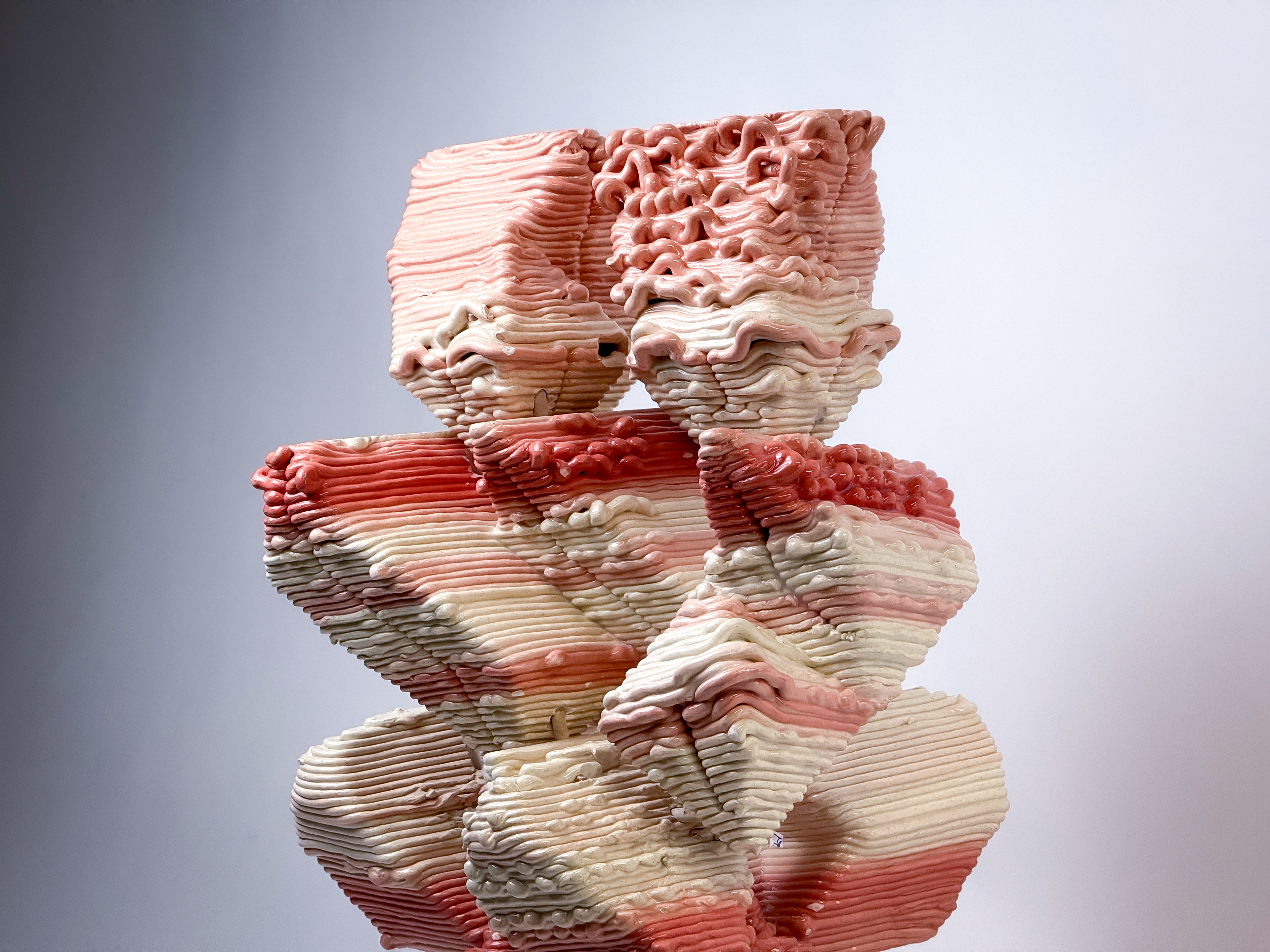
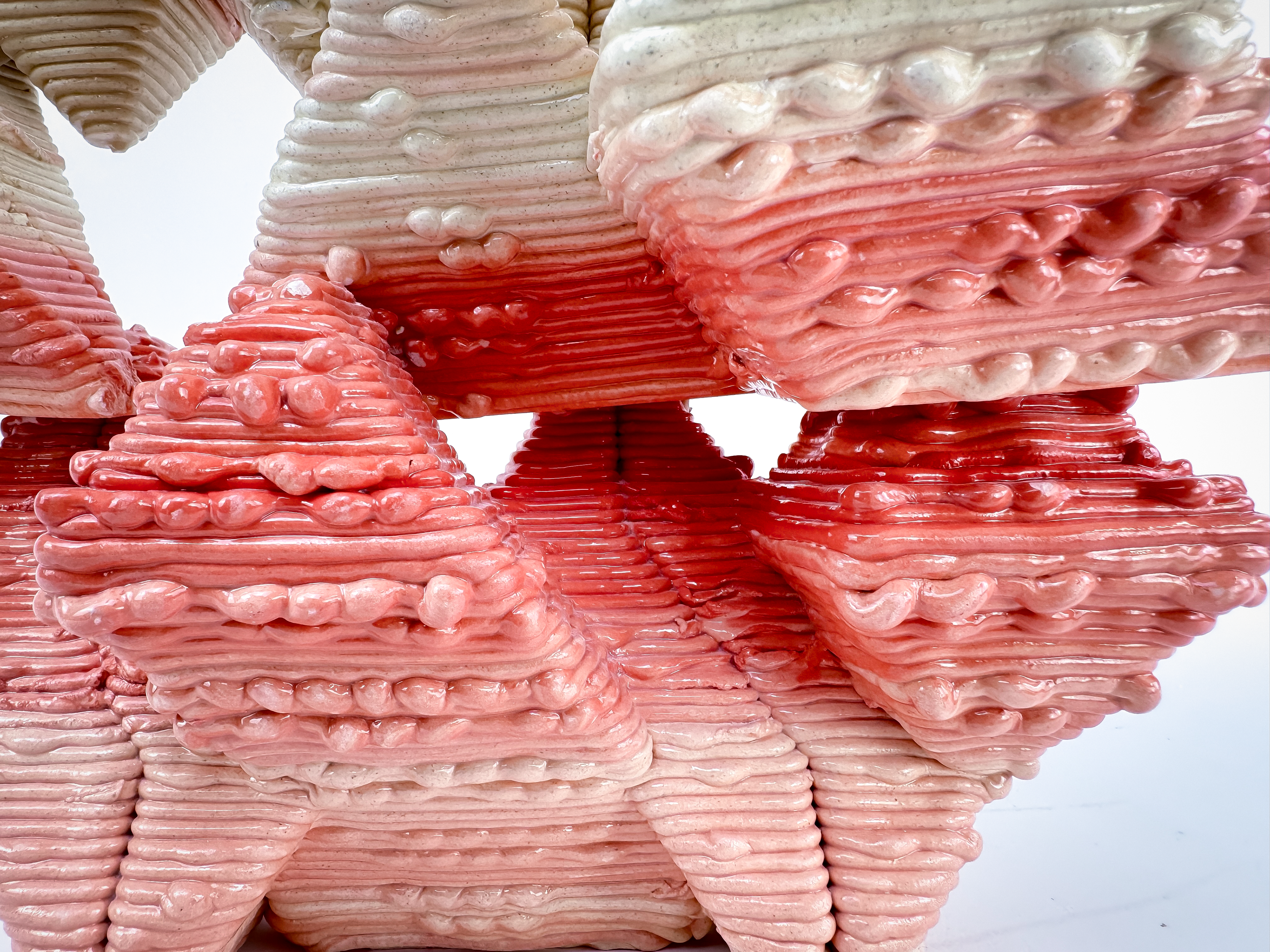
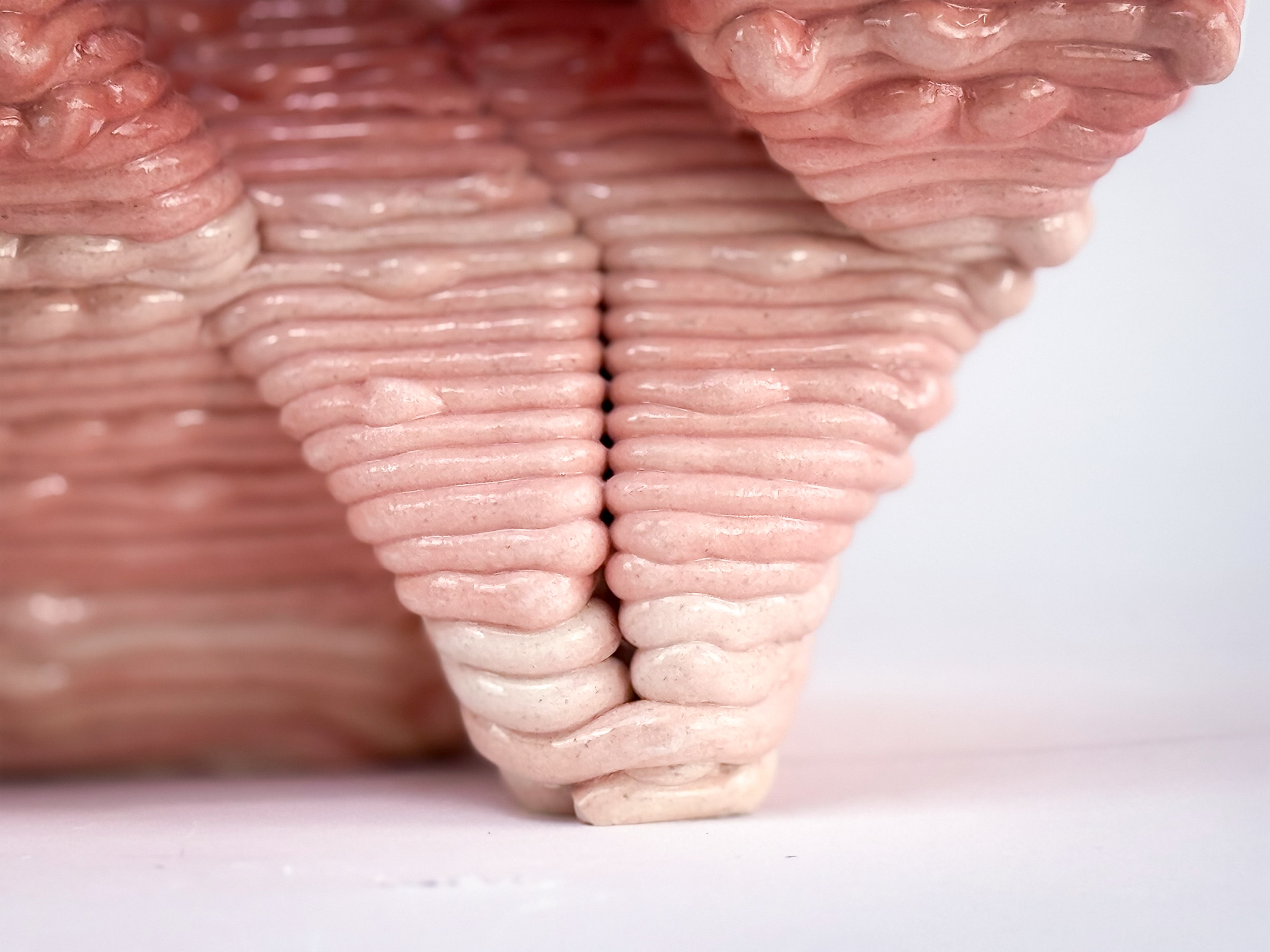
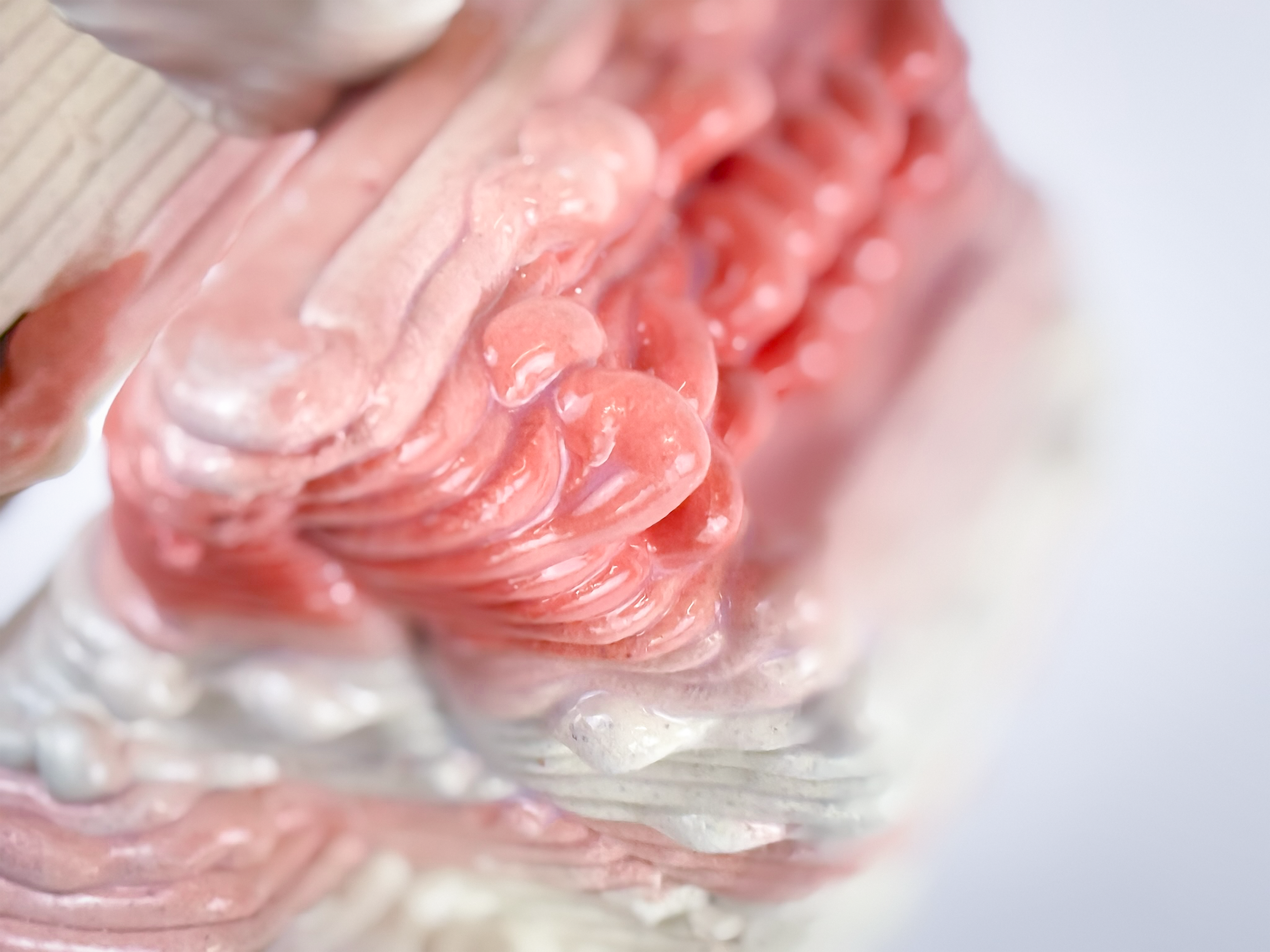
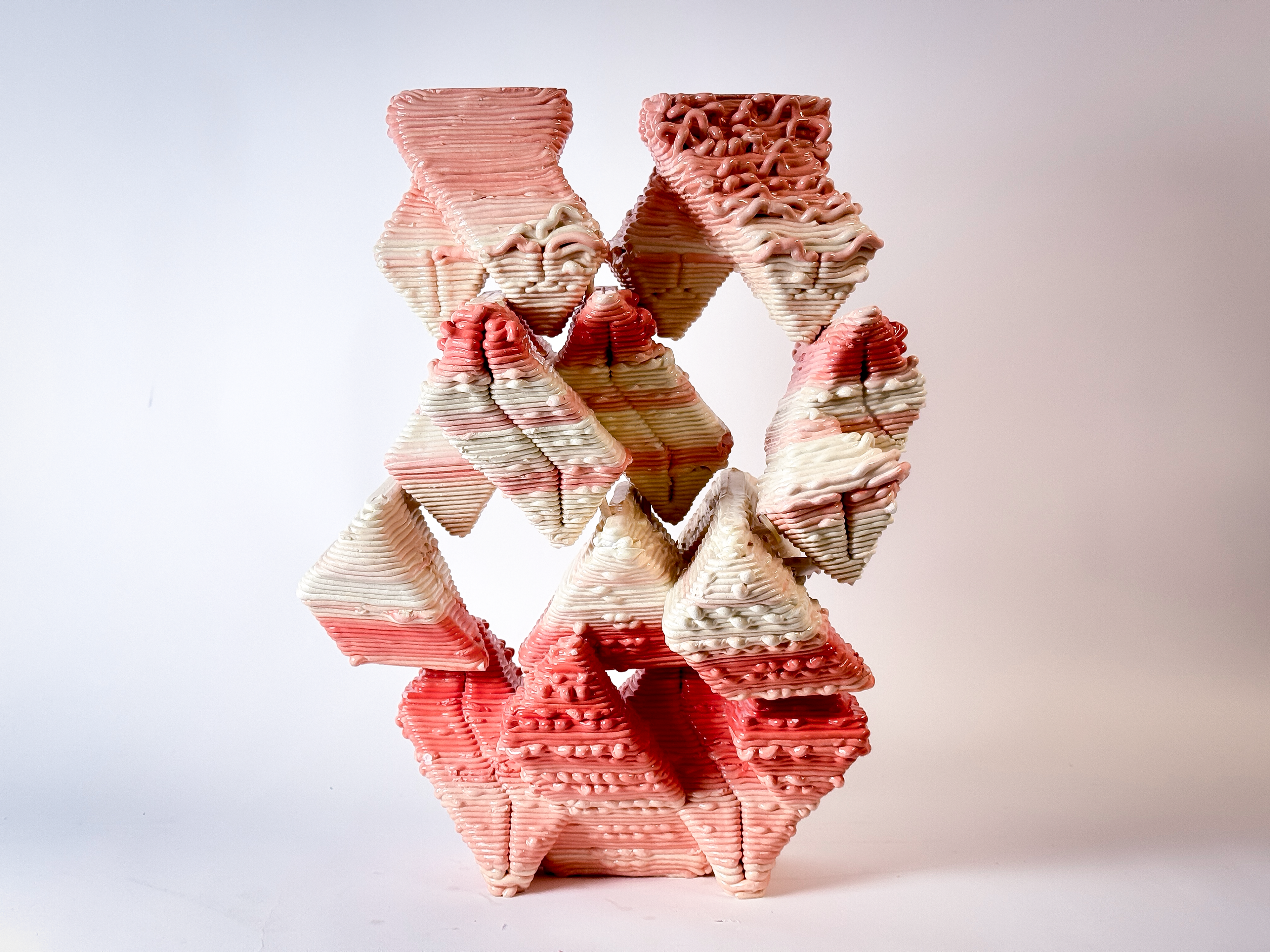
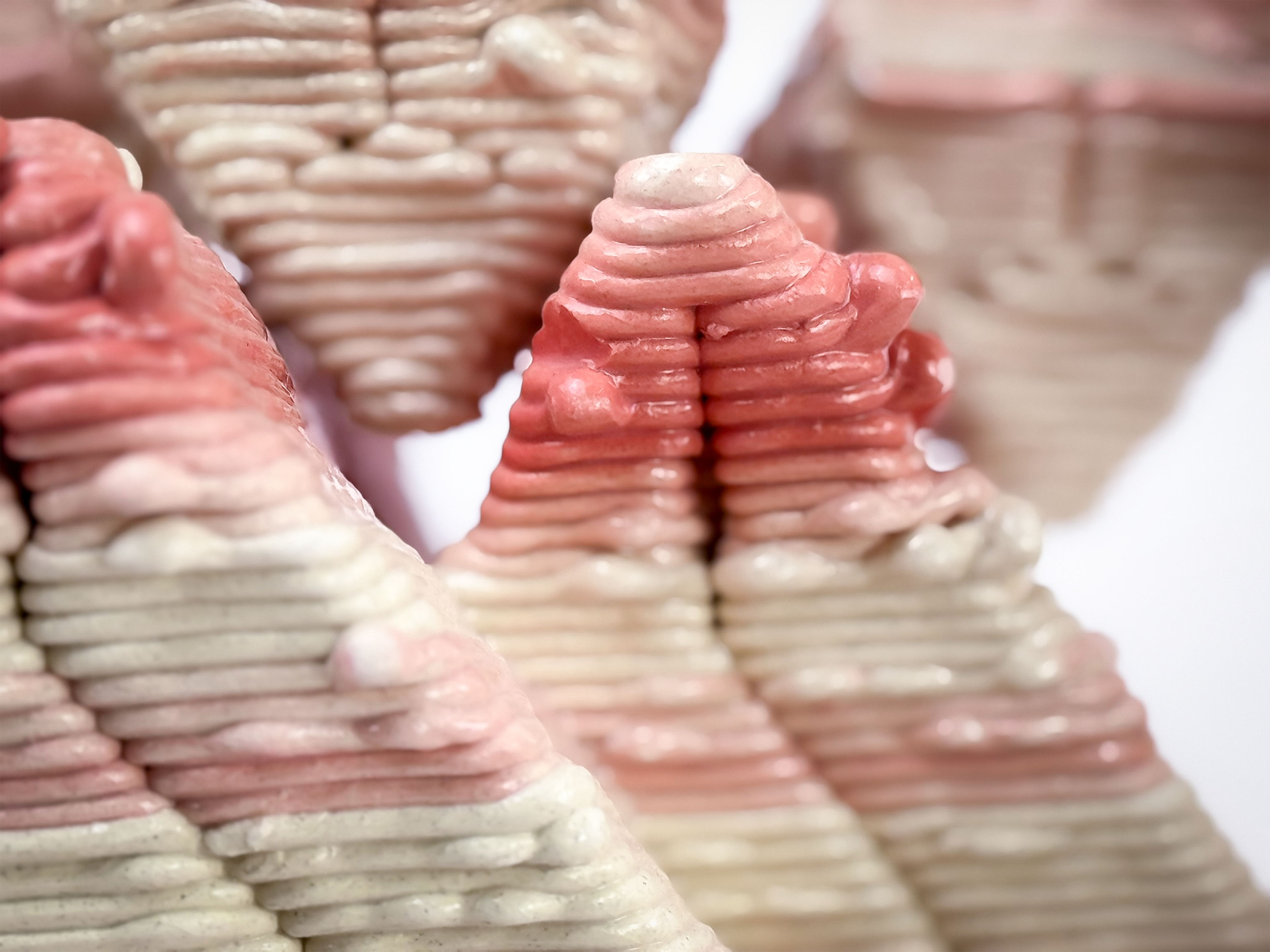
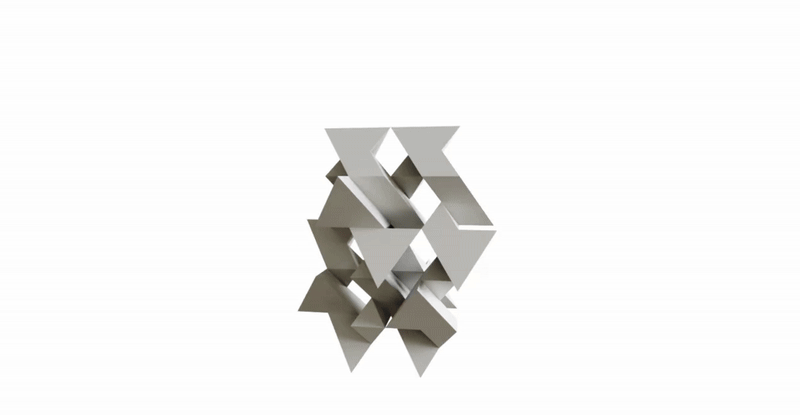
Master of Science in Design: Robotics and Autonomous Systems (MSD-RAS)
Weiztman School of Design, University of Pennsylvania
ARCH 801 Material Agencies _ Fall Semester
Instructors: Andrew Saunders & Jeffrey Anderson
TAs: Claudia Campuzano & Nicholas Houser
MSD-RAS Program Director: Robert Stuart-Smith
ARI Robotics Lab Operators: Nicholas Sideropoulos & Shunta Moriuchi
Team Lobster: BurcuGocen, CarinaJoseph, CongruiGao, DaxlerZou